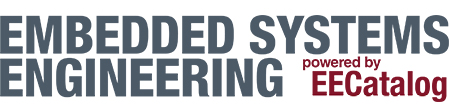
“…managed complexity”: Q&A with JC Ramirez, ADL Embedded Solutions
October 18th, 2017
By Anne Fisher, Managing Editor at EECatalog
Editor’s Note: With a technical background that includes Navy nuclear plant supervision, nuclear instrumentation, semiconductor product development and embedded systems engineering, JC Ramirez, VP of Engineering at ADL Embedded Solutions, Inc. is well positioned to share with EECatalog readers his perspective on trends in the embedded small form factor space. “We have some exciting things we’re anticipating in the coming year,” Ramirez told us. “For example, we’ll be taking a CoaXPress card and a PC/104 form factor SBC and demo-ing 4k video at greater than 30 frames per second embedded vision to the military,” he went on. “That’s exciting being in early on the move to 4k for the military sector.”
Benefits of adopting a holistic approach to the complex puzzle of managing performance, power and other factors for small form factor embedded vision applications
Ramirez also described a recent surveillance use case (see side bar). Edited excerpts of our conversation follow.
EECatalog: What new trends in the embedded space designers and developers should be aware of?
JC Ramirez, ADL Embedded Solutions: With respect to small form factors the continuing (not just new) trend is to take these rugged small form factor systems and make them smaller, and smaller, and smaller. It seems like every three years they are losing another couple of pounds and a few more inches in striving to meet the enclosure’s demands.
Mission computers that used to be rackmount are now being asked to be smaller than 6 x 6 [inches] per side, and the overall weight has gone from tens of pounds to single digits. At this point we’re talking less than five pounds and less than three pounds—depending on the particular application.
The challenges are the same, but what is new is the fact that they are just getting harder and harder to meet, with the continued trend toward smaller and lighter.
EECatalog: On what recent project has ADL has seen some of those challenges?
Ramirez, ADL Embedded Solutions: One of our latest and greatest products in the embedded vision space involved ADL and Euresys getting together to make a PCIe/104 small form factor CoaXPpress frame grabber. Euresys then went further, wrapping the combined frame grabber and CPU stack in a MIL-STD 810 chassis from ADL, qualifying it over an extended temperature [-40 ºC to +85 ºC] range, and certifying it for MIL-STD 810 operation.
To offer a bit of context here, the military always lags the consumer space a little bit and [with regard to] next-generation vision systems—we’re talking frame grabbers, cameras, displays—they are only just now to the point where they are ready to adopt 4k video resolution vision systems. They need the frame grabbers and the computers to be able to pull that off. That’s the next generation of products that you are going to see in the military space for vision and for displays and cameras.
Euresys brought to the project its whole history of knowledge about CoaXPress and CameraLink, most of which has been on the factory floor. Recognizing the mechanical and temperature constraints, it is in this area that ADL leveraged its knowledge along with experience in rugged applications in the military space. The collaboration between ADL and Euresys was a no-brainer.
It is not something ADL could have done on its own. We needed to go find a frame grabber expert that knew the high-performance frame grabber part of it and CoaXPress in particular.
EECatalog: What factors went into the decision by Euresys to choose ADL for its CoaXPress frame grabber?
Ramirez, ADL Embedded Solutions: High-performance frame grabbers require a lot of resources from the CPU: PCI Express lanes, which is the primary way that we would interface to a frame grabber and also computing power. As the project began, ADL had the highest-performance PCIe/104 Intel® Core™ I7 SBC on the market, and, not only that, we already had a longstanding vendor-client relationship with Euresys. We had history with them with CameraLink. They knew of us, they knew of our product line; they knew of our military legacy.
Use Case: Long-distance Surveillance
Asked to share an example of a use case which included some particularly tricky requirements, Ramirez told us:
“A long-distance surveillance application that is high-altitude is one we came across recently. Because it was high altitude there was very little in the way of cooling available in the surrounding air, so it had to be completely fanless and rely 100 percent on conduction cooling.
The complexity of that design because it was surveillance related, high-performance embedded vision required a CPU that needed complete customization, not so much because the functionality was not readily available, but because the space constraints were such that we needed to collapse as many of the features as possible into one or two boards.
That is probably as complex as it gets. It’s manageable complexity that emphasizes the factors that go into a holistic design. We had a very small space that we needed to work with; the high-performance requirements were ridiculous; and it was high altitude.
The design had to be done in a very particular way, where we could achieve the high performance and yet direct all the heat directly into the cooling plate of the system, which was then directly mounted to the structure of the aircraft—it does highlight what we’ve been discussing, it’s all interconnected.”
EECatalog: Is there too much or too little emphasis on particular things as the goal of getting smaller and lighter is relentlessly pursued—what are the tradeoffs?
Ramirez, ADL Embedded Solutions: Let me speak to some of the key design relationships. When we are talking about the challenges for doing a small form factor rugged design we are usually in the realm of high-performance, where, for example, it might require a very fast multicore CPU that draws a lot of current and power and therefore generates substantial heat, which now needs to be managed.
The relationship goes something like this—the higher the performance, the higher the heat, current and power requirements, and therefore the complexity of what must be managed increases.
And, inevitably, the more you have to do to manage power, the bigger that chassis gets and the heavier it gets. So, the only way to manage that—I sometimes use the word holistically—you really have to manage all the factors at the same time.
More often than not, we’re building small embedded computers but for a group of software guys tasked with certain missions, and they may not always be familiar with what the relationships are at the hardware level. Their reaction can be to ask for the absolute highest performance with the absolute highest memory and the absolute highest storage requirement.
However, recognizing that there is a big difference between a quad-core computer and dual-core computer, a big difference between an Intel Core machine and an Intel Atom machine is crucial. What should be avoided is spec’ing in requirements without enough knowledge about or acknowledgement of what some of the other constraints, and what thermal management will be needed, for example. Questions to ask include: What’s the environment; do you guys have any airflow; do you have no airflow? Is the box standalone; Is the box attached; Can you do something where we can do conduction cooling and help bring the size of your enclosure down? And all of these questions pretty much have to be addressed in parallel at the same time so that somehow, someway, you can find the best balance between all of these things and come up with the smallest embedded computer that still meets the performance requirements for what the client needs.
EECatalog: Do you see a need to push back against the trend, if am understanding correctly, to tend toward focusing on one or two goals, say high-performance, without seeing the big picture? Why is broader knowledge necessary?
Ramirez, ADL Embedded Solutions: As mentioned earlier, it is a complex, iterative process, so what we do for our customers is not so much offer COTS products, but offer COTS building blocks where we have, for example, MIL-STD 810 chassis in various sizes that help cover three-quarters, 80 percent of the rugged small form factor opportunities that come our way. We know that the remaining 15 to 25 percent are going to be full custom from the ground up—the situation just dictates that.
We are able to satisfy half of our customers with COTS building blocks that we customize in some way, shape, or form, and for the other half ADL solutions are 100 percent custom from the ground up. We start with the specs of how big, how heavy, what’s the I/O, what is the environment, and we design it from scratch.
About JC Ramirez
JC Ramirez is VP of Engineering and Product Management at ADL. JC (BSEE, MBA), has a technical background that includes Navy nuclear plant operation, nuclear instrumentation, semiconductor product development and embedded systems engineering.